From basic wire to custom cable harnesses, connecting the system is as important as the system itself.
Innovation requires a certain level of flexibility; this much is obvious when we look at the development of new technology as a whole industry. However, that same method of thought is rarely applied to the electrical components and cables space. When the end product is a large scale or mass-produced item, the electrical components are sourced, which leads to price wars and often turning to Asia for sourcing. However, new design, industry specific applications, or even new industry requirements all present challenges which ultimately require customized solutions that won’t be resolved in the traditional high volume, lowest cost space.
In recent 2016, an OEM customer faced a design challenge that they could not solve through modification of current applications. They had all of the piece parts necessary to complete a GPS tracking system for an automotive application, but no reliable way to integrate the system. As at the time, there were no existing standard cables available for this specific application.
The customer hired the engineering and manufacturing team Star Werks, Inc. who worked closely with them to develop a cable harness that allowed the GPS receiver to be connected to their product.
Because installation was going into an automotive application, all of the connectors were required to be of a securing type. To guarantee the cable harness would be robust enough to function reliably in an automotive environment. It was decided to use a two-step process for molding the main connector back housing. The first step in the process was to do the pre-molding with a solid resin (PE) to lock the wiring in place to prevent stress in the critical area where the wires are connected to the terminals in the connector.
Pre-molding process |
The second (and final) step was to perform the over-mold using a PVC material. The softer PVC material combined functionality with the aesthetics of a nice softer textured surface. As the pre-mold secured the internal wire structure, the over-mold allowed the design of a flexible strain-reliever, supporting the cable.
Because of this, the stress from bending and pulling in different directions would not cause damage to the cable, in the area where cable interfaced with the connector housing. Note: For shielded cables, it can be desirable to place copper foil between the pre-mold and over-mold to maintain the shielding. During configuration of the cable and wiring, it is possible to include other items like a small power converter into the connector, which on this case provides the 5-volt required for the GPS. A fragile wire connection, designed into a robust custom cable.
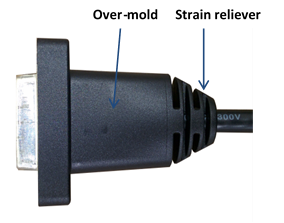
Verification of design and process for a pre-molded and over-molded connector.
About Star Werks, Inc.
Star Werks, Inc. is a Chicago-based single point manufacturing solution provider, partnering with customers to offer customized solutions for sourcing, manufacturing and design requirements that improve bottom line. With nearly three decades of experience, Star Werks has served both domestic and international customers, providing services including PCBA, turnkey assemblies, custom molded cables and wire assemblies, custom power supply and engineering services.